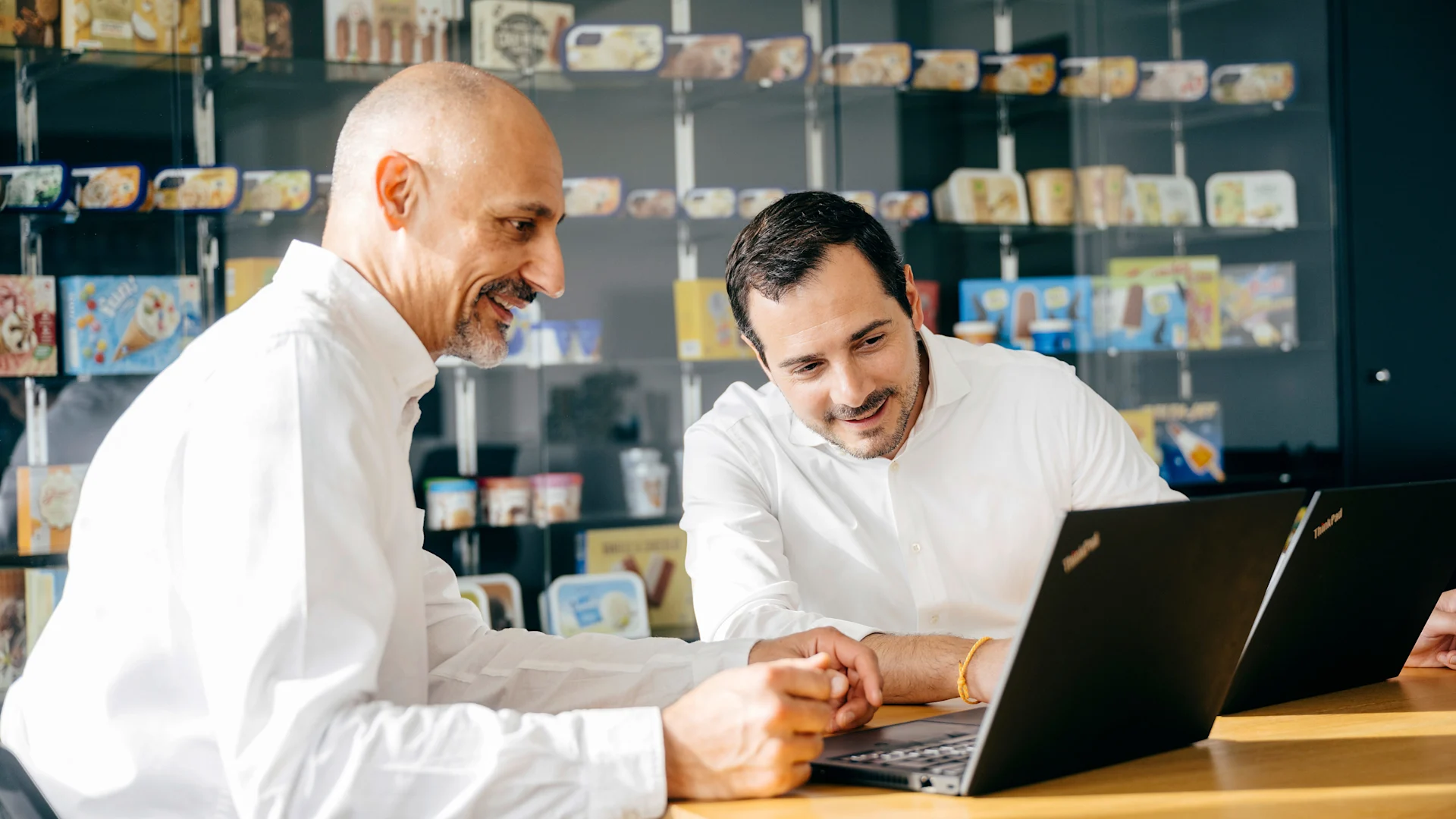
Work environment
Downshifting in your career
More time for yourself: Why a senior executive voluntarily decided to hand over his position to a younger person.
navigation
Quality Control
Melanie Senti and Nathalie Moravetz are responsible for the safety of non-food products at Migros. We accompanied them on one of their inspections.
Two turquoise parrot candles are in the shopping trolley, next to boxes with a string of LED lights and a razor. Coloured children's modelling clay, bottles of scented oil and a red silicone cake tin are also visible. Melanie Senti and Nathalie Moravetz manoeuvre the full trolley through the aisles and stop in front of a shelf of charcoal grills - for CHF 15. «Wow, that's a bargain,» says Melanie Senti.
The two women are responsible for the quality and safety of the products in the non-food section. Melanie Senti is a quality assurance specialist at the Federation of Migros Cooperatives (MGB). Nathalie Moravetz heads the non-food laboratory of SQTS, an analytical service provider that also belongs to MGB. Today they are on a shopping spree in Pizolpark in Mels (SG). They are buying more than 40 non-food products at Do it & Garden, Micasa, Sportxx, Melectronics and the Migros supermarket - for almost 500 francs.
This shopping spree is called product range control in technical jargon. This is to ensure that Migros only sells products that meet the legal requirements and its own quality standards. «Products that are available for purchase in Migros can be checked up to four times – as samples, before the product launch and several times afterwards,» says Senti. That is the regulation.
It must be demonstrated that each individual product complies with safety and quality specifications before it goes on sale. Once the products are on the shelves, they are checked to see if everything is still compliant – through controls by the authorities or by Migros itself. «Our product range control is based on random samples. We focus on products with a high risk, such as electrical appliances and toys,» says Senti, who trained as a chemical laboratory technician and studied food technology. Toys or craft supplies can be tricky because of problematic constituents, electrical appliances because of possible malfunctions.
The two checkers go on shopping trips several times a year, each time to a different branch. They also regularly put costume jewellery in the shopping trolley because of the nickel content, which could trigger allergies if too high. Textiles, candles and products that come into contact with food are also usually on their shopping list. And this time, the barbecue for 15 francs also ends up in the shopping trolley.
Nathalie Moravetz brings the grill together with the other purchased items to SQTS in Dietikon. Swiss Quality Testing Services was founded in 1930 by Migros, it is independent and works for various clients. 120 employees test products for safety, constituents and hygiene - also in the area of food and food packaging (see box). At the entrance to the non-food laboratory are three futuristic plastic legs. «This is where stockings are tested for fit,» says the lab manager. The lab tests, for example, plasticisers in plastics and heavy metals in toys. There is even a candle test room. Moravetz's team lets the purchased parrot candles burn down completely. «It can happen that decorative candles don't burn down in a controlled way, and simply melt uncontrollably», says Moravetz. That could lead to complaints or even become dangerous because it is a fire hazard. Additionally, the burning time and soot behaviour are tested.
The grill is brought to the technical laboratory Although the test managers don't grill any sausages here – they always do that before grills are even sold – the inexpensive grill is nevertheless closely scrutinised according to a predefined test plan. The tray, for example, is heated to check that it does not deform. The experts also check the grill grate for constituents because it comes into contact with food, the stability of the legs and even the packaging and instructions for use.
Melanie Senti and her colleagues in the MGB's quality assurance department also check whether the non-food products they buy are correctly labelled. «With cosmetics and chemicals, for example, it happens time and again that important instructions for use or danger warnings are missing,» says Senti. In addition to her, seven quality assurance officers work in the non-food area – in the food area there are four.
Senti's team also decides what to do with defective products. «We assess the risks and recommend what action to take.» Depending on the defect, the supplier may have to make improvements, the product could be withdrawn from sale or a recall even launched. «In the case of withdrawal, the products are removed from sale.» With a recall, customers are asked to return goods that have already been sold. «This happens when the defect is so serious that the health and safety of consumers is at risk,» explains the checker. As was recently the case with a child car seat that could not be adequately secured. «In the event of a recall, products are immediately blocked from sale and recalled,» says Senti. In 2020, there were six recalls of non-food products.
The inspection of the inexpensive grill did not reveal any serious defects. It has a firm stand and the grill tray is heat-resistant. However, this does not hold true for the label with the warnings on it. It turns brown after repeated heating and becomes illegible. The instructions also lack a parts list. «We have already discussed with the supplier how and by when it will correct the defects,» says Melanie Senti. There were also only a few complaints about the other 40 non-food products from the product range check. «That is not always the case,» says Senti, who is already planning the next shopping trip with colleague Moravetz.
The Migros food range is checked regularly. The quality assurance staff at MGB also work closely with SQTS. About 20,000 products a year are checked to see whether they meet the legal and Migros-internal safety and quality requirements.
The inspections are risk-based and carried out on a sample basis. Special attention is paid to delicate products. If there are discrepancies, corrective measures are defined with the suppliers or internal processes are initiated.
Discover exciting stories about all aspects of Migros, our commitment and the people behind it. We also provide practical advice for everyday life.