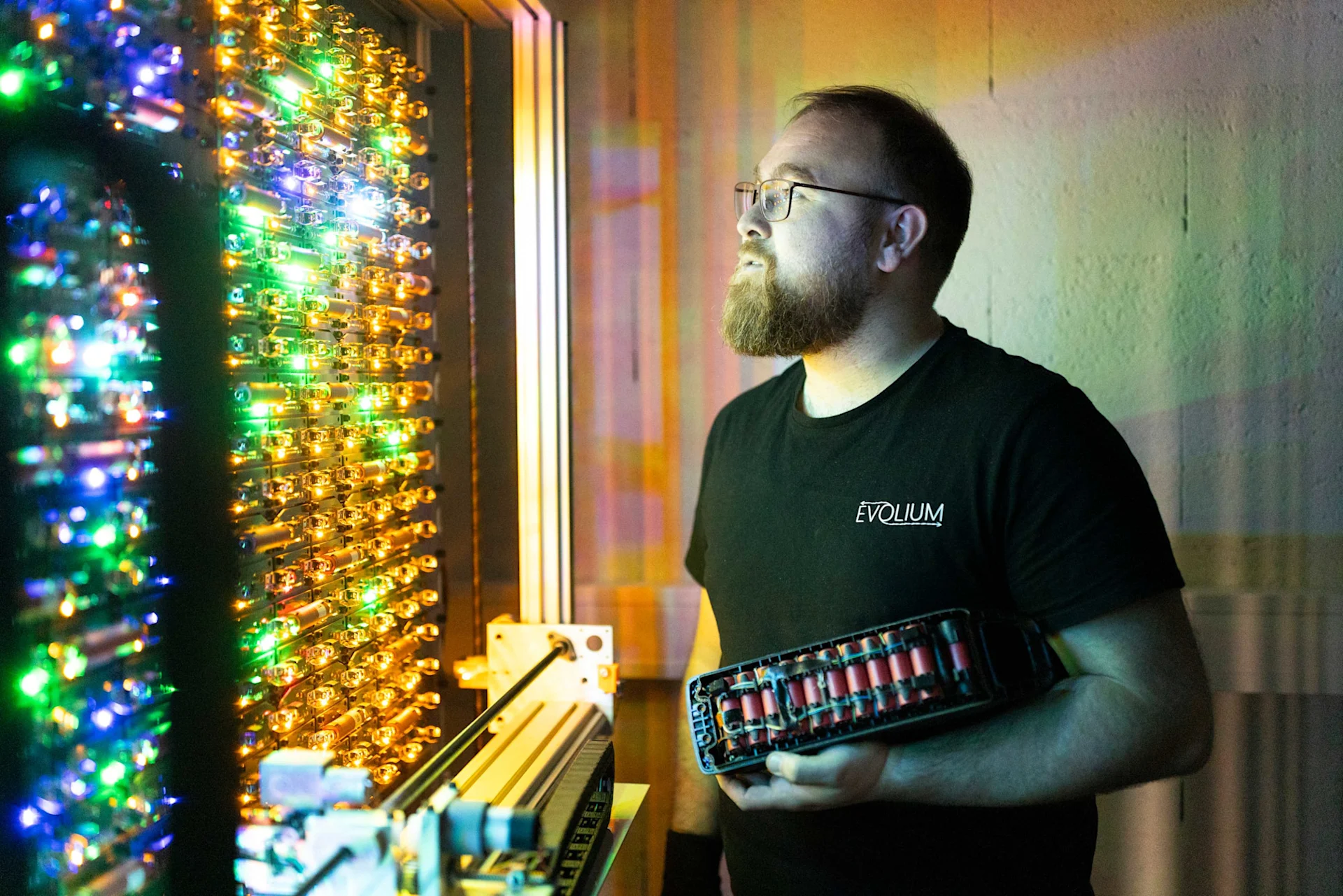
Migros Pioneer Fund
Rechargeable lithium batteries that last longer
With the support of the Migros Pioneer Fund, Evolium Technologies is extending the life of lithium batteries.
navigation
Packaging
The Basel-based start-up Mycrobez produces biofoam from fungus and wants to encourage the packaging industry around to the globe to think more circularly.
In the lab, there are transparent bags filled with a fibrous brown mass that looks like a ball of wool. What grows here in the cellar of a terraced house in Basel is a fungus. Its food: organic waste. The final result is a material that has similar properties to synthetic foam, such as polystyrene: it is very light, has an insulating effect and is resilient. However, it also features the great advantage that the raw material literally shoots out of the ground, because the biofoam is based on fungal root mesh or mycelium. What’s more, an even greater benefit is that it is 100 percent biodegradable and can be processed into fertiliser.
Three resourceful young entrepreneurs from Basel are working on sustainable packaging material with their start-up Mycrobez. “Our vision is to change the packaging industry by moving it away from harmful disposable materials that pollute our natural world toward components that remain in the natural cycle,” explains co-founder Moritz Schiller (23). Their biofoam can completely decompose in a month. Compostable packaging would be a particular blessing for countries without a recycling system.
Four years ago, Moritz Schiller and Mosas Pilscheur helped their friend Jonas Staub with his matriculation project. It revolved around a 3D printer that could print fungal cells. They were 19 years old at the time. “Up until that point, the only fungus I had given much thought to was the mushrooms that we eat. However, fungi are fascinating organisms that have been performing various functions essential for overall survival for one and a half billion years, and are the reason that life on land is possible”, says Schiller. In fact, the mushrooms on your plate are only the fruiting body. Underneath, you’ll find the mycelium, a fine root network that supplies the fungus with nutrients.
The fungus fascination never left the young men, and because they had time after graduating, they continued to tinker – in Mosa’s father’s wine cellar spanning three square meters. They ordered edible mushrooms on the Internet to grow themselves, extracted the mycelium and mixed it with organic waste such as bean stalks. The mycelium ate through the culture medium and grew into a mass, the mycelial composite. The three men experimented with humidity, temperature, oxygen and CO₂, and to their own amazement, they had a kind of foam in their hands after a few weeks.
After the first successful tests, they began researching and found that they were not the first to extract biofoam from fungus. This material is already produced in the USA, but the mycelium is implanted into the culture medium by hand there. The Basel-based company understood that the process had to be fully automated if biofoam was to compete with polystyrene in terms of price and volume. Only then could it actually become an attractive alternative for the industry. Another obstacle on the journey to mass production lies in the nature of the material. Organic materials depend on the original product: corn foam requires corn, algae film needs algae. “Being dependent on raw materials in production means being at the mercy of supply and price fluctuations,” Schiller explains.
Mycrobez has achieved a coup in this respect: they have bred a fungus that flexibly adapts its digestive enzymes to the respective types of organic waste. Waste from wooden pencil production, threshing residues, sawdust and waste from food production such as bean stalks or coffee bean skins can be used – the end product is always fungal foam. Mycrobez currently purchases raw material from large companies in the local food and agricultural industry.
Since biofoam also takes on various properties, it can be used in a variety of ways across industries: for example, as noise or heat insulation in the construction industry, because unlike polystyrene, it is not self-combustible. It can also be used in the furniture and design industry or in the luxury industry to make boxes for watches, pens or flacons. However, Mycrobez has its sights set primarily on applications for the packaging industry, where Schiller believes a sustainable impact can be achieved most quickly by generating much less plastic waste.
The start-up is currently financed by partners, private investors and sponsors, including the Migros Pioneer Fund. The young company has grown to 17 employees and has its own laboratories and workshops. It is perfectly situated in the roadmap defined after founding. The goal is not to become a manufacturing company, but rather to make the production process available adapted to the corresponding application and country, i.e. to sell licenses.
The start-up now works with globally active partner companies for versatile applications in several industries. The world’s first natural foam that can financially compete with polystyrene is expected to be available in 2025. Mycrobez could thereby actually herald the new sustainable packaging standard.
Do you know what can go in the bin? With our tips and tricks, recycling not only becomes easy, you also save a lot of waste.